Robot-assisted In-situ Inspection
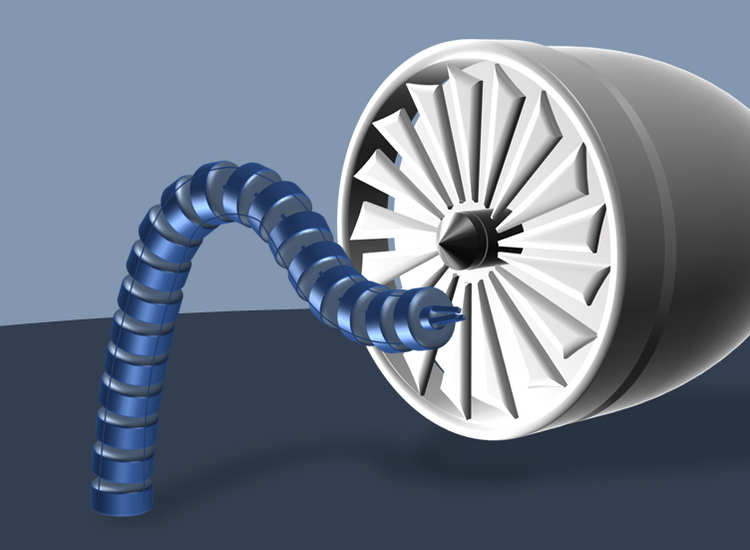
E-Mail: | tim-david.job@imes.uni-hannover.de |
Team: | M. Sc. Martin Bensch, M. Sc. Tim-David Job |
Year: | 2020 |
Funding: | Bundesministerium für Wirtschaft (BMWi) |
Duration: | 01.03.2020 - 31.12.2021 |
During In-situ aeroengine maintenance it is necessary to inspect the blades inside the turbine. A boroscope is currently used for this, which is inserted into the respective gas channel through a small opening on the turbine side (equivalent to endoscopy). The assessment of the turbine blades is greatly influenced by the rigid boroscopes used and their possible poses in the gas duct. Continuum robots, on the other hand, are characterized by high mobility and small dimensions and, in addition, not only enable intuitive operation, but also the reproducible approach to poses.
The aim of this research project is to develop a new type of continuum robot that enables the turbine blades to be examined using a fringe projection system on the end effector. The project is being carried out in cooperation with the Institute for Measurement and Control Technology. The complete development of the measuring system at the top of the robot is carried out by the IMR. After the requirements have been clarified together, a robot concept is developed taking into account the kinematics or statics modeling. In addition to the design and manufacture of a robot that is used exclusively for measurement purposes, stiffening mechanisms are examined in order to later enable higher process forces to be absorbed. In addition, a simplified model of a turbine is built, which serves as a test environment for the experimental evaluation of the continuum robot.